Driven by the impact of the COVID-19 pandemic, we’ve seen skyrocketing shipping prices and delays at major ports causing frustrations to importers at all corners of the globe. The future of the industry is now uncertain – and nobody knows when things will return to ‘normal’.
But how did it come to this? In an era where demand for international exports is so high, why is there such a container shortage? We explore the complete story below.
Why is there a container shortage?
In short, there is a global container shortage because the shipping and logistics industries were sorely unprepared for the shocks created by the pandemic.
Cancelled voyages causes crisis
In early 2020, when the pandemic spread throughout the world, China and a whole raft of other countries locked themselves down. Economies came to unexpected halts, production of goods ceased, and once busy metropolitan areas became little more than ghost towns. Demand for goods fell dramatically.
As a result, major shipping lines cancelled a raft of scheduled voyages, significantly reducing the number of ships flowing to and from ordinary routes. This not only put a halt to the routine flow of goods. It resulted in empty containers not being collected.
Typically, container ships operated in a cycle - bringing loaded containers to ports, unloading them, and taking empties on backhaul routes. But this flow was suddenly interrupted. At the ports of Los Angeles and Long Beach, for example, empty containers piled up rapidly as 41 vessels cancelled deliveries between mid-February and early April 2020.
These empty containers would have usually ended up in Asia, but instead they remained where they were.
China opened, but the world remained closed
As the world tried to cope with the harsh impacts of the pandemic, China began to recover. The Asian nation was therefore able to get back to its trade routines, but other countries couldn’t.
Lockdowns in critical port cities meant that containers full of cargo simply could not be returned to Asia – where they were desperately needed.
In India, for example, lockdowns led to massive backlogs of containers in places like Chennai and Mundra as dockworkers couldn’t attend work to unload them. Truck drivers also couldn’t collect cargo from these ports. The entire India east coast backlog reportedly escalated to 50,000 boxes.
Massive reductions in shipping capacity also meant empty containers remained in places where they normally wouldn’t. In the Port of Melbourne, for example, empty containers piled up as not enough shipping lines were operating to transport them back to China. Shippers scrambled to deal with oncoming detention and demurrage charges, as their container were left in ports unattended.

Demand shock intensifies the crisis
Out of nowhere, the international demand for goods skyrocketed as people in lockdown around the world purchased goods in droves. Ocean shipping liner Hapag-Lloyd stated that it was the “strongest increase in (container) demand, following one of the strongest decreases in demand ever”.
A surge in demand for COVID-19-related products, for instance, placed great pressure on global supply chains. In May 2020, the Organisation for Economic Co-operation and Development (OECD) reported that the demand for face masks at the time “might be ten times higher than world production capacity”.
The pandemic fuelled online shopping, and such demand was reflected in the profits enjoyed by the e-commerce industry. In the United States alone, consumers spent $791.7 billion, up from 32.4% in the previous year. Online giant Amazon also enjoyed an annual revenue of $386 billion in 2020 (up from $100 billion in the previous year), resulting in an 84% profit.
Shippers could not (and still cannot) secure containers easily
The result of the ‘demand shock’ was that regular businesses struggled greatly to secure shipping containers to export their products. These struggles remain a major challenge today.
Steel boxes are now harder to find than ever before, as containers are either piled up in terminals or are stranded in the ocean on ships who are waiting to unload at overloaded and congested ports.
· U.S. based Agriculture Transportation Coalition reported in August 2021 that 22% of their members’ sales were lost simply because they couldn’t access containers to get their cargo overseas.
· Seaway Intermodal, an Australian exporter of citrus fruits such as oranges and mandarins, reported that it was difficult to secure refrigerated shipping containers (or ‘reefers’) they needed for export. Once they finally did, the trick then became “finding plug space on the vessels where the refrigerated containers can continue their cold treatment right through to market”.
· Rice exporters in Southeast Asian nations like Vietnam and Thailand reportedly cancelled their shipments altogether. This was due to the “impossibility of securing containers” as empties piled up elsewhere in places like India, Australia and New Zealand.
· Port congestion has meant containers are literally stuck on vessels, forced to wait waiting months before they are unloaded. For example, delays and congestion increased the time it takes for a container to arrive from Beijing to Chicago from 30 days to over 70 days.
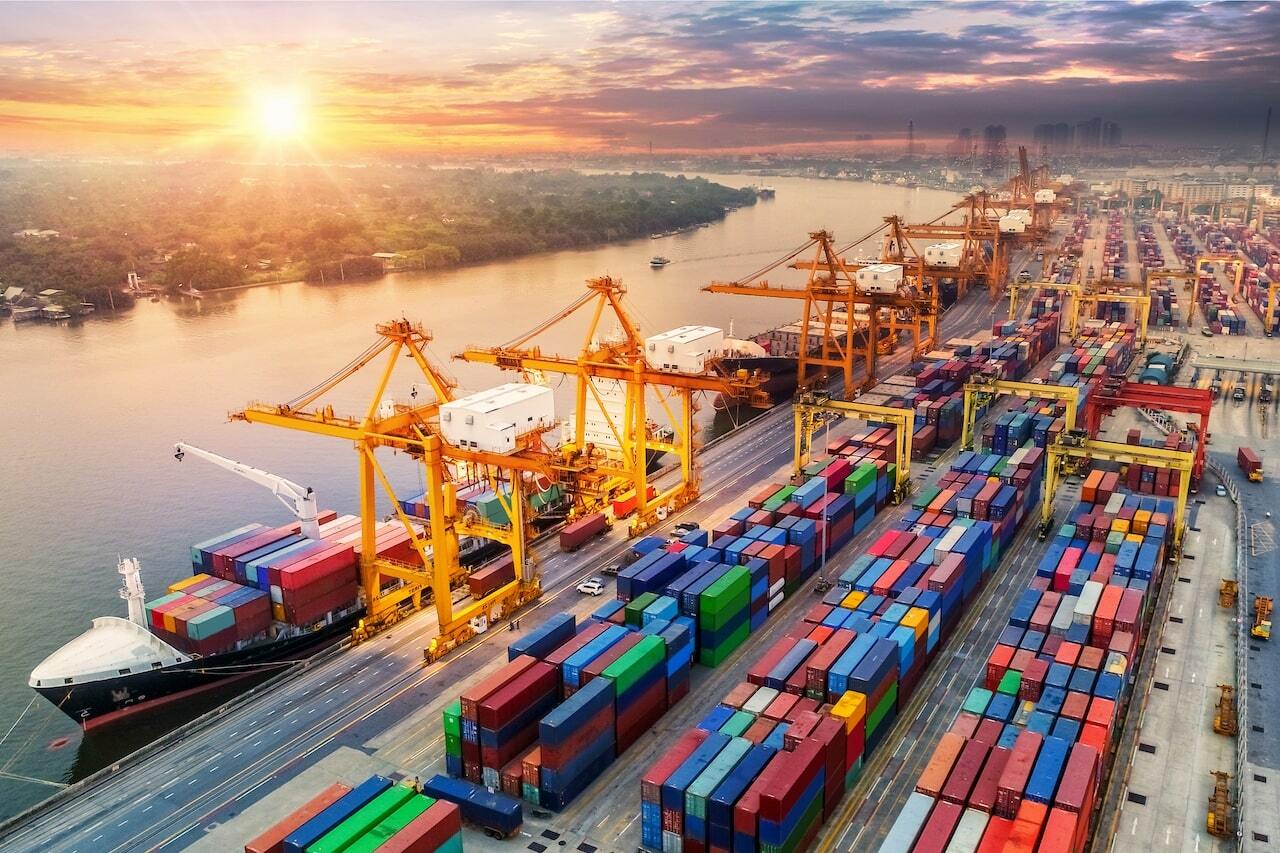
Containers become woefully expensive
Constrained carrier capacity, surging demand and a colossal container shortage have all combined to skyrocket the price of a container. This is happening everywhere around the world.
· In February 2021, shippers moving goods from Asia to Europe reportedly paid six times more for a container than what they did in April 2020. According to one index, rates escalated to USD $8,455 per 40-foot container – the highest recorded by that index since its creation in 2016.
· Rates from Asia to the West Coast of the United States were also four times higher compared to March 2020, landing at an astonishing USD $4,709 per container.
· From Asia to the East Coast, rates more than doubled to rates of USD $5,658 per container.
· Sabrini Foods, an Australia food importer, reported that a container that cost $600 before the pandemic “was now worth $2,000 and could reach $4,000 and beyond.”
· A Full Container Load (FCL) from China to the United States used to cost between USD $3,000 to $5,000. At the time of writing, it now costs between USD $14,000 to $15,000.
The future of shipping containers: when will the crisis end?
Nobody in the industry has a way to accurately predict how the shipping crisis will come to an end.
Some companies have introduced their own container booking service to try and make it easier for exporters to secure containers. Cainiao, owned by Alibaba, is one of those companies – launching a service to expand to over 200 ports in 50 countries.
But here is no doubt that shippers will need to think differently about streamlining their supply chain. This will involve booking their shipments well in advance, and perhaps using a mixture of air freight and ocean freight to facilitate their transactions.
Businesses that ship internationally are strongly encouraged to seek expert guidance in order to navigate this unparalleled global shipping crunch.
If you need help navigating the present container shortage, speak to our freight forwarding experts at The Sourcing Company.